A changing world
For the past number of years, we have seen vast changes in weather conditions with scorching summers, wildfires, floods, storms, and so much more as a result of climate change.
At OFP, this has got us asking the questions what is really happening and how can Timber Frame homes help slow down the effects of climate change?
Let’s start by setting the scene.
According to the UN, climate change refers to long-term shifts in temperatures and weather patterns. Since the 1800s, human activities have been the main driver of climate change, primarily due to burning fossil fuels like coal, oil and gas, accounting for over 75 per cent of global greenhouse gas emissions and nearly 90 per cent of all carbon dioxide emissions.
This year alone, June 2023 was confirmed as the hottest June in the UK since records began in 1884, and July saw the world’s hottest day with heatwaves across many parts of Europe, China, and the US.
Not only do we see a rise in temperatures, but we also have had unpredictable disasters worldwide, such as wildfires in Greece, monsoon flooding in India, and Tropical Storm Mawar hitting Japan, Guam, the Philippines, and Taiwan.
The built environment and construction sector accounts for 38% of global carbon emissions, and it’s estimated that globally, we build the equivalent of a city the size of Paris every week.* And so with that, the construction industry has got a part to play.
The UK’s road map to net zero came into full effect on 15 June 2023 when Building Regs Part L, Conservation of Fuel & Power, states that we must reduce carbon emissions by 31% for new homes through a set of reformed insulation and air tightness requirements with the long term goal of reaching a 75-80% reduction in CO2 by 2025.
At OFP, the construction of any building should be done with the environment in mind. However, we go one step further than that and believe that not only should the building be conducted in a way that reduces carbon footprint and uses sustainable materials, but that the building itself should have a positive effect on the environment when in use.
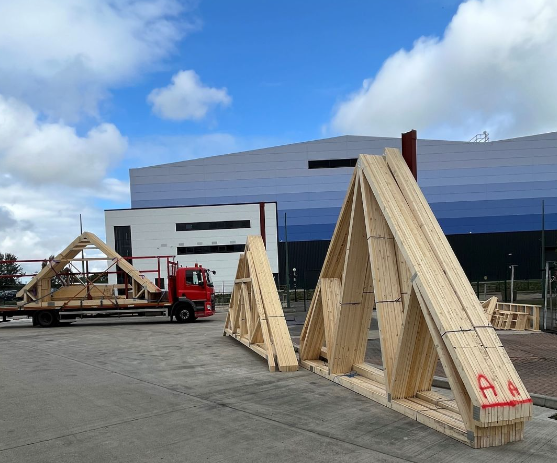
Reducing CO2 during build
Timber Frame construction lends itself well to utilising Modern Methods of Construction (MMC) such as off-site manufacturing. MMC is known to dramatically reduce CO2 emissions through embodied carbon, which is the CO2 produced during the design, construction and decommissioning phases of development.
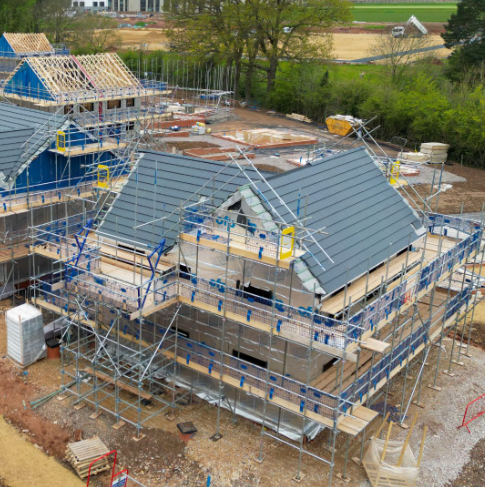
OFP is already delivering off-site manufacturing solutions across Kent and the home counties. We are proud to have a purpose-built, off-site manufacturing facility in Kent. We produce all our trusses, floor joists, panels and more in our factory, ready for assembly on-site.
Energy-efficient homes
Not only can CO2 be reduced during the build, but wood also has a lower thermal conductivity compared to concrete, steel-frame and masonry construction; therefore, timber frame can create energy-efficient homes that yield long-term positive effects for homeowners and the environment.
Regarding reducing the global average individual carbon footprint from 6.3 tons (2020) to 2.1 tons in 2030, as recommended by experts, home energy is a significant area of opportunity. *** Timber frame homes are airtight and highly insulated, which can be particularly beneficial as it can be easier to keep your home cool during summer and heat up faster in winter, which has cost-saving benefits.
So, the more energy efficient the building is, the better for the environment.
What are OFP doing?
We understand and recognise that any business has an impact on the environment. Like everyone, we want to do our part to reduce this impact and work in a sustainable and environmentally friendly way. This is why we have adopted MMC into our business processes, ensuring less waste, high accuracy and precision.
We also use renewable energy to power our office and factory through solar panels, turning waste sawdust into pellets and burning them in our biomass boiler.
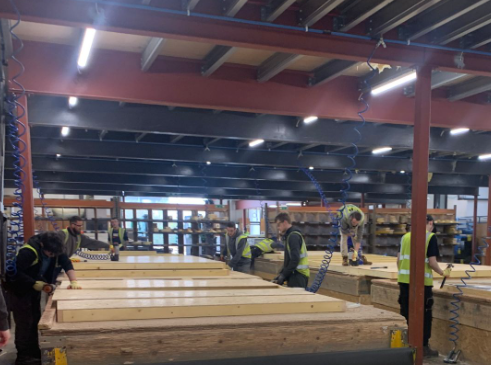
We are keen to reduce, reuse and recycle wherever possible. This includes reusing timber offcuts by joining them together using a technique called finger jointing to make full wood panels, which can be used again.
For more information, check out our ESG page.