OFP Timber Frame is ready to deliver off-site manufactured timber frame solutions to aid the changes we’ll see coming from the 2025 Future Homes Standard and Future Buildings Standard.
An interim step towards the movement in recent times is the changes to Part L (conservation of fuel and power) of Building Regulations which came into effect on 15 June in the form of two new approved documents.
- CO2 emissions are to be reduced by 31%
- a new emphasis on concerns over thermal bridging leading to heat loss and condensation.
The construction industry has an essential part to play in making this happen, and one fundamental way to do this is through off-site manufacturing and modern construction methods.
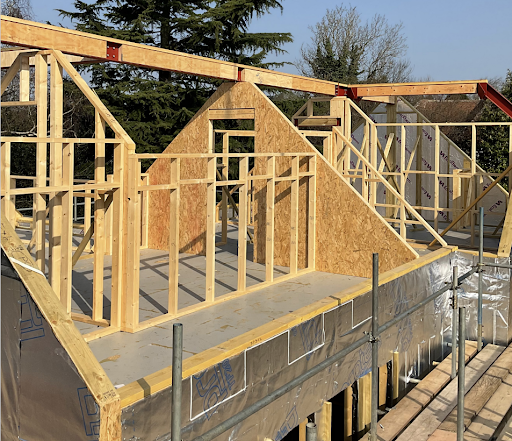
Timber Frame Off-Site Manufacturing in Kent
What is Off-Site Construction?
Off-site construction can also be referred to as ‘prefabrication’, ‘off-site manufacture’, or ‘modern methods of construction.’
Off-site construction involves the process of planning, designing, fabricating, transporting and assembling building elements for rapid site assembly to a greater degree of finish than in traditional piecemeal on-site construction.
OFP are already delivering OSM solutions across Kent and the home counties and are ready for the future changes. At OFP, we are proud to have a purpose-built, off-site manufacturing facility in Kent. We produce all our trusses, floor joists, panels and more in our factory, ready for assembly on-site.
One of the significant benefits of timber frame structures is that they are precision engineered, making them incredibly strong and durable. At OFP, our pre-fabricated panels are made in factory conditions in a controlled environment and the precise engineering involved in the process results in very high levels of consistency. This level of control and accuracy leads to projects being delivered on time and on budget every time.
Benefits of off-site timber frame construction
1. Time-Saving
A three-bed house built with timber frame can be air and water-tight within a working week from delivery of the timber frame. Thus less damage and waste are likely to occur on-site.
A four-storey block of flats built with a timber frame can save up to 50% on build time, meaning tenants can move in sooner, and the return on investment can be realised quicker.
This fast erection time is due to a substantial amount of construction in the factory, with only final assembly necessary on-site.
This also allows plumbers, electricians and other trades to get in and work within the building, regardless of the outside conditions, allowing for a more predictable construction schedule.
2. Thermal efficiency of Timber Frame
Timber is a natural insulator and aids reduced energy levels in all buildings. Timber frame buildings far exceed those built using traditional materials regarding thermal efficiency and go way beyond Building Regulation requirements. Furthermore, a timber frame building is also economical to run due to its ability to heat up quickly and retain that heat for longer.
3. Environmental Impact
A new report,’ Whole Life Carbon Assessment of Homes’, published by the Advanced Industrialised Methods for the Construction of Homes (AIMCH), concludes using sustainably sourced timber-panelled MMC methods to build new homes rather than masonry products can reduce the carbon impact of construction.
Timber frame has the lowest CO2 cost of any commercially available building material. For every cubic metre of wood used instead of other building materials, 0.8 tonnes of CO2is saved from the atmosphere.
A typical 100m2, two-storey detached timber frame home contains 5-6 cubic metres more wood than the comparable home built using traditional methods.
And the environmental benefits continue after construction. The thermal efficiency of timber means that a timber building will remain warmer throughout the winter, reducing heating costs and staying cooler during the summer months.
Other benefits include:
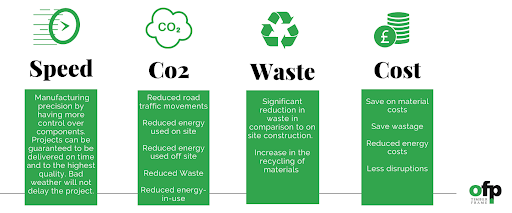
Not only can OFP Timber Frame design and manufacture your timber frame kit, floors, and roof trusses, but we can also manage and erect your project through our in-house Contracts management teams.
For more information on the off-manufacturing process and our facilities and services, Click here.