How does it affect Timber Frame Structures?
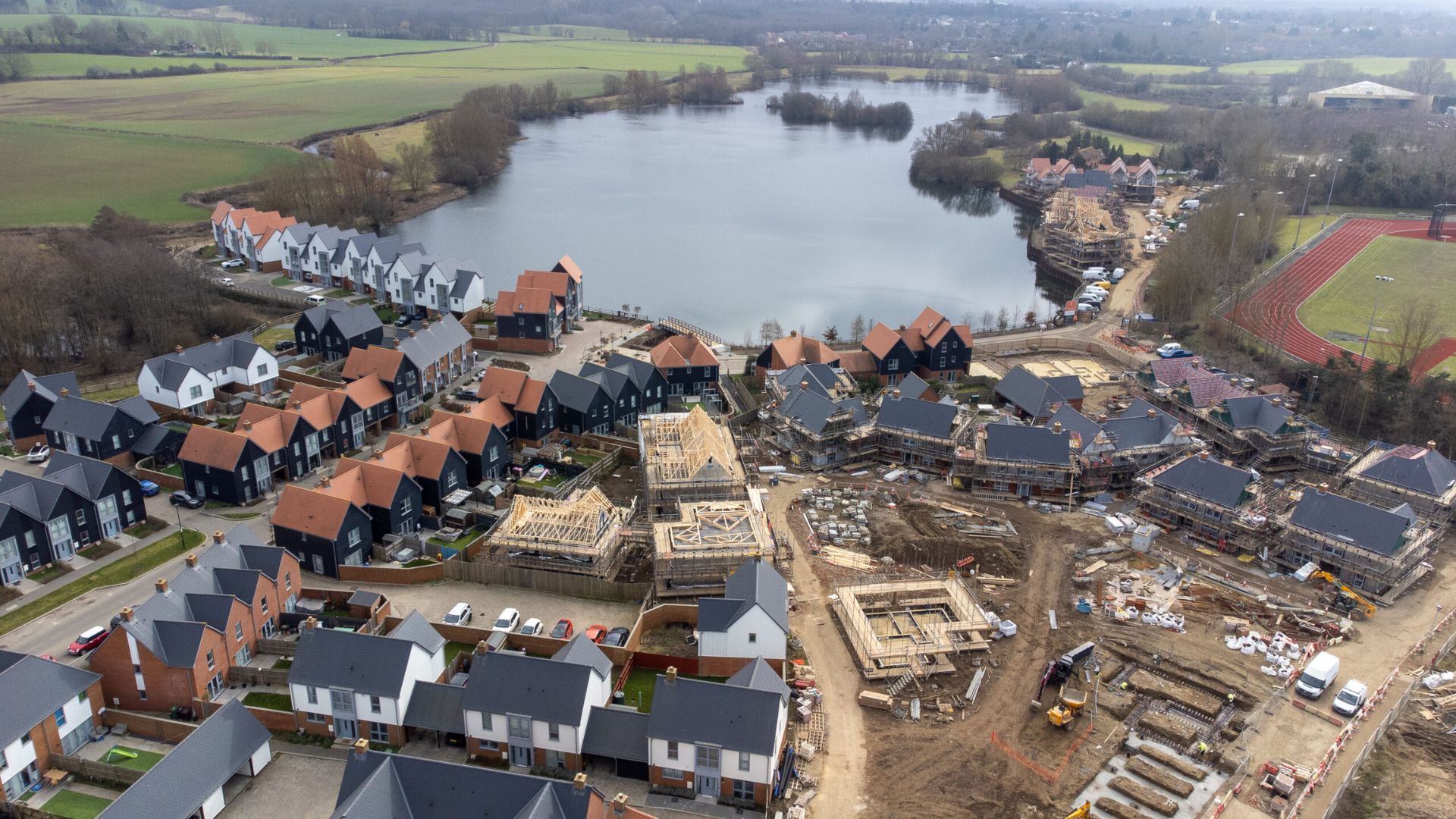
Pictured project: 300 houses in Conningbrook, Ashford, Kent
What is Part L Building Regs?
If you are in the construction industry, you will likely have heard about the changes to Building Regulations Part L. These came into effect on 15th June 2022 as an interim step towards the goal of 75-80% reduction in carbon by the Future Home Standards.
The interim steps are to:
- Reduce CO2 emissions by 31%
- Put a greater emphasis on concerns over thermal bridging leading to heat loss and condensation.
How does this impact future building design and timber frame structures? This is something we are asked on a daily basis, so we wanted to help answer those burning questions. In this article, we will explore what OFP Timber Frame is doing to adhere to and lead the way in embracing changes in Building Regulations Part L.
How does it affect timber frame design?
Timber frame is a sustainable material with incredible thermal efficiency and the lowest CO2 cost of any commercially available building material, so that is already a good start. Still, it goes another step further and provides excellent insulation and helps to contribute to the U-value of the building. Let’s look at this a bit further and what OFP can do to help.
Insulation & U-Value
Part L has requirements for the thermal performance of a building. At OFP, we are bespoke in our approach to timber frame. This means we can offer various solutions to suit our clients’ needs. With the change in Building Regulations Part L – the external wall u-value is changing to be more efficient. We work with the technical teams of insulation, membrane and timber suppliers to offer options to comply with fire, SAP, structure and acoustic needs.
Timber frame walls can incorporate hi-spec insulation that contributes to a wall U-Value. Using a combination of factory-controlled measures and low lambda value insulation, a great U-Value can be achieved through a slender wall – saving space and weight in the project.
Our core offering is typically a pre-installed rigid PIR board within the panel. See below:
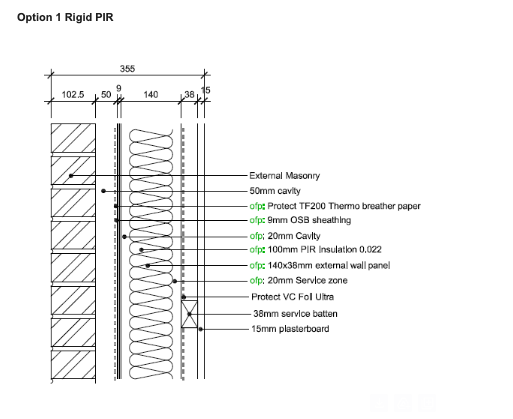
Our second core offering is a full-fill stud using site-fit mineral wool. See below:
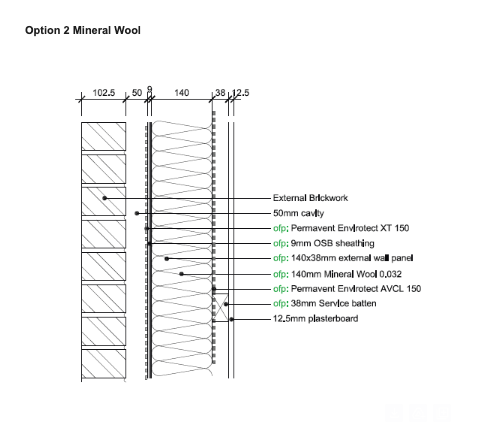
Finally, our third core solution is achieved by working closely with Actis to provide a site-fit solution using a hi-tech combination of multi-foils.
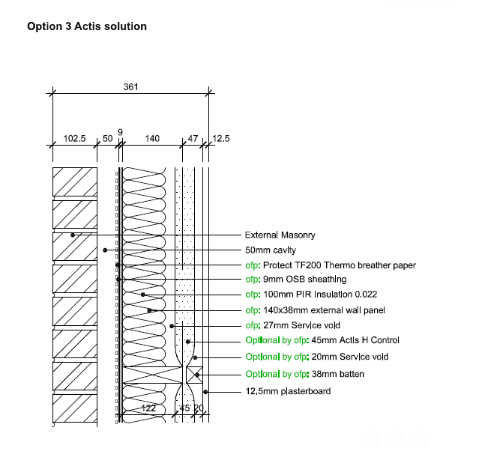
What does this mean for your project?
Timber frame provides a solution that incorporates thermal performance, air tightness, and low carbon technology – all using a renewable and sustainable building material. The main structure of the project will be made using a product that locks in CO2, uses responsibly sourced FSC and PEFC certified timber, is lightweight and quick to install, and gets the required low U-Value needed to comply with Part L and beyond.
At OFP, we do not have just one solution. We have many options and are very flexible, working closely with architects, designers and developers to achieve what they need to accomplish. This approach helps to not only create comfortable homes that are efficient but also cost-effective for the homeowner.
Visit our website or contact us directly:
Contact
T: 01304 613298