It’s no doubt that advancements in technology and offsite manufacturing (OSM) are having a positive impact on the construction industry. We previously looked at the benefits of offsite manufacturing to not only the industry but also the environment.
Now we go one step further to show the adaption of OSM through the use of innovative technology at OFP. Through the automation of processes and procedures, we are able to exceed levels of accuracy and efficiency like never before.
We are already delivering OSM solutions across Kent and the home counties. We do this by producing all our trusses, floor joists, panels and more in our factory which are then transported ready for assembly on site.
Let’s take a closer look at the technology behind the automation that make this happen:
Hundegger Speed-Cut SC3
The Hundegger Speed-Cut SC3 is a highly accurate multi-axis saw which runs centrally through our factory. It is programmed directly from the CAD design providing highly detailed and accurate results.
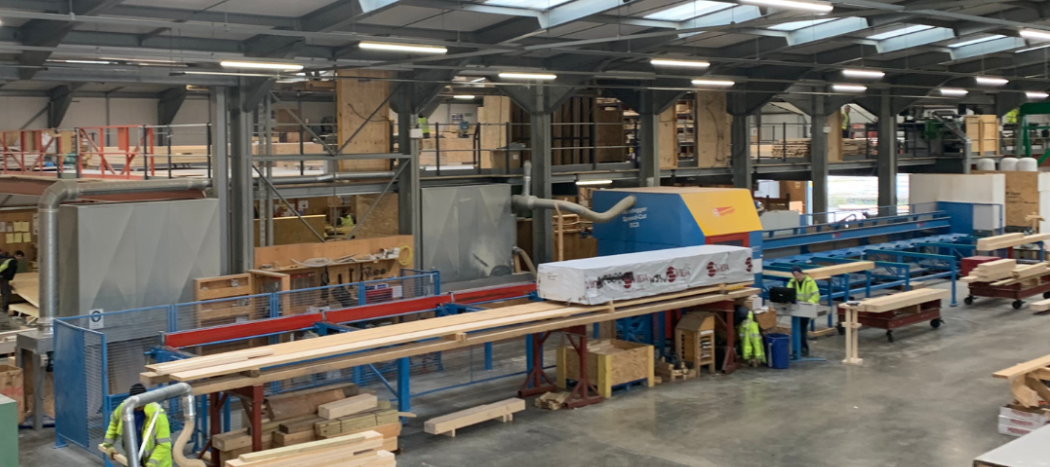
This saw allows us to cut holes, birds mouth, notches and more many other details. It runs using two conveyor systems, bringing speed and precision to the fore.
This fantastic machinery allows us to do complicated and exciting architectural design works accurately with fewer work operations.
Check out our Pippin Barn project, where we used this technology to bring the architect’s vision to life.
CNC saw
Our CNC (computer numerical control) saws allow us to automate the movement of our primary saws. It can be programmed from the CAD model, created by our in-house designers, to cut precise lines and detailed shapes and curves.
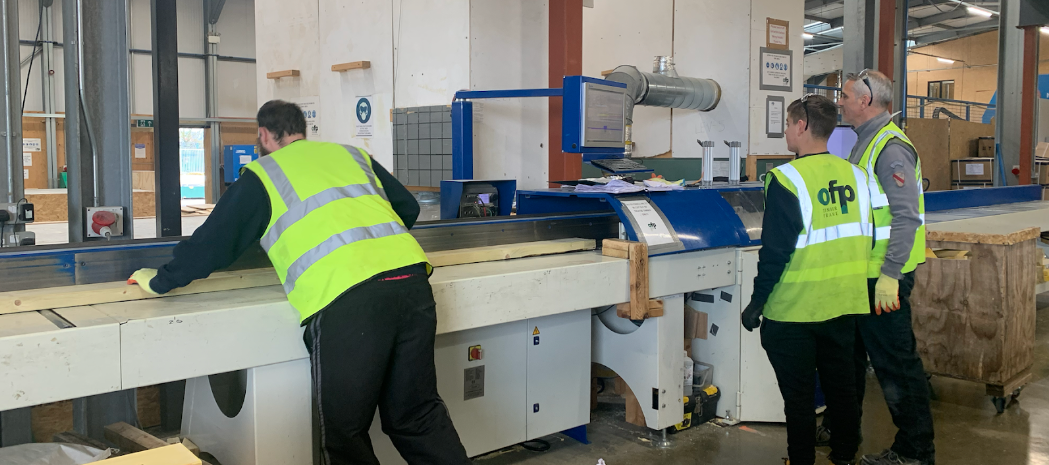
This level of precision allows us to quickly and accurately cut materials; reducing energy consumption, reducing the risk of human error whilst increasing safety in the workplace.
It is very important to us that we utilise this technology in an optimal way giving us a typical material yield above 95%, thus reducing the amount of wastage from the manufacturing process.
Open web joist press
Open web joists are floor joists that are made up of v-shape metal struts. They are engineered using specialist software which allows them to span further than alternative timber products. This also aids access for follow on trades to carry out their works. The joist press uses powerful hydraulic pressure to roll over and press the plates into the timber for a speedy, safe and accurate manufacture.
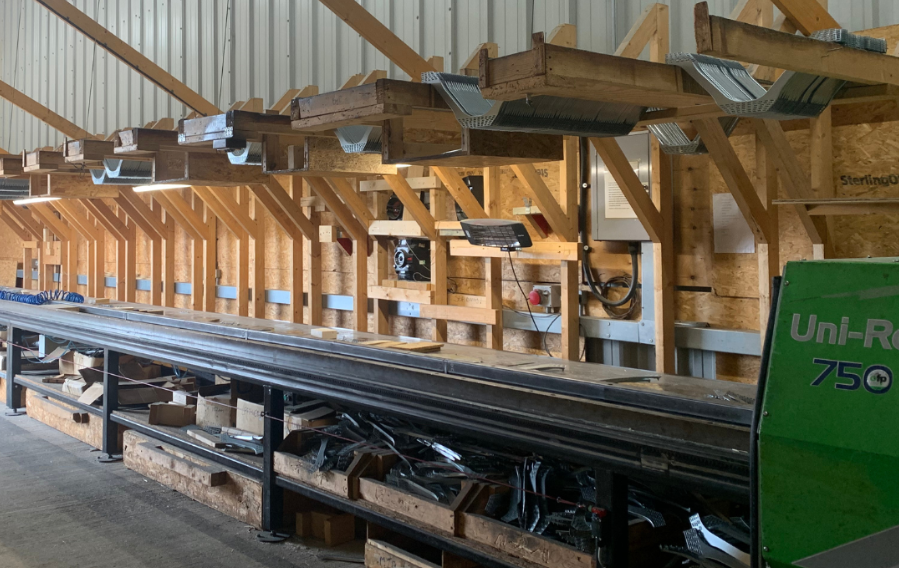
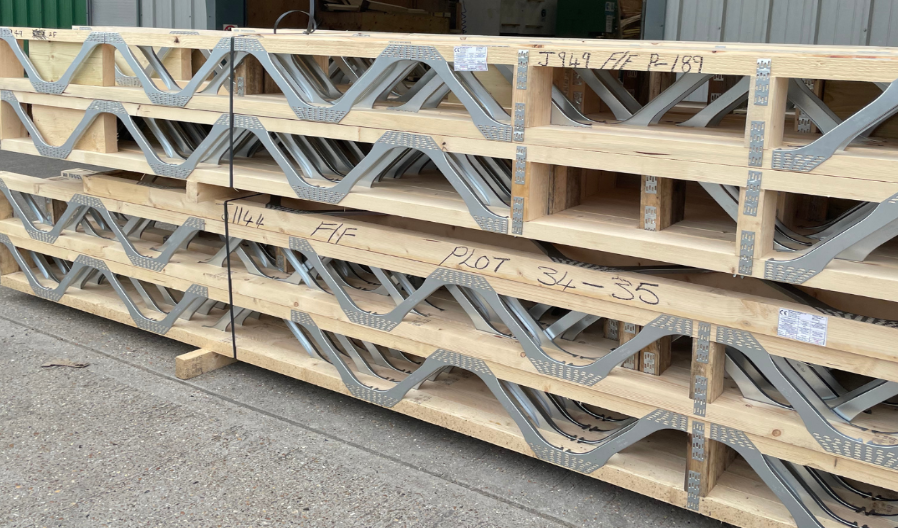
Truss press
Our truss press uses a ‘C’ hydraulic clamp mounted on an A frame.
The jig works in a certain way which makes it is easy to unload and manoeuvre trusses safely both in the factory and onsite.
The trusses are accurately set out using maglock pedestals on a steel floor.
Our truss press boasts a start/stop function to reduce the electrical running costs which helps us to be as sustainable as possible and reduce our carbon footprint.
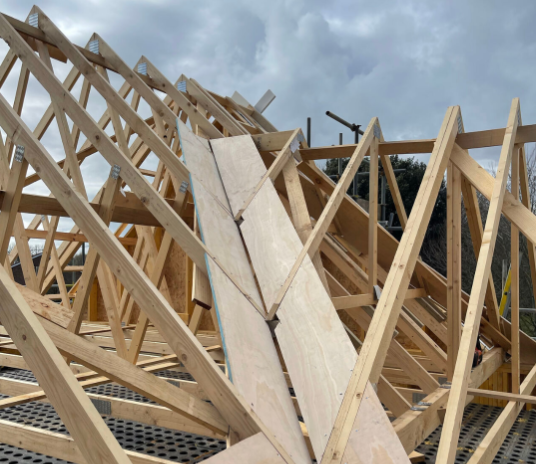
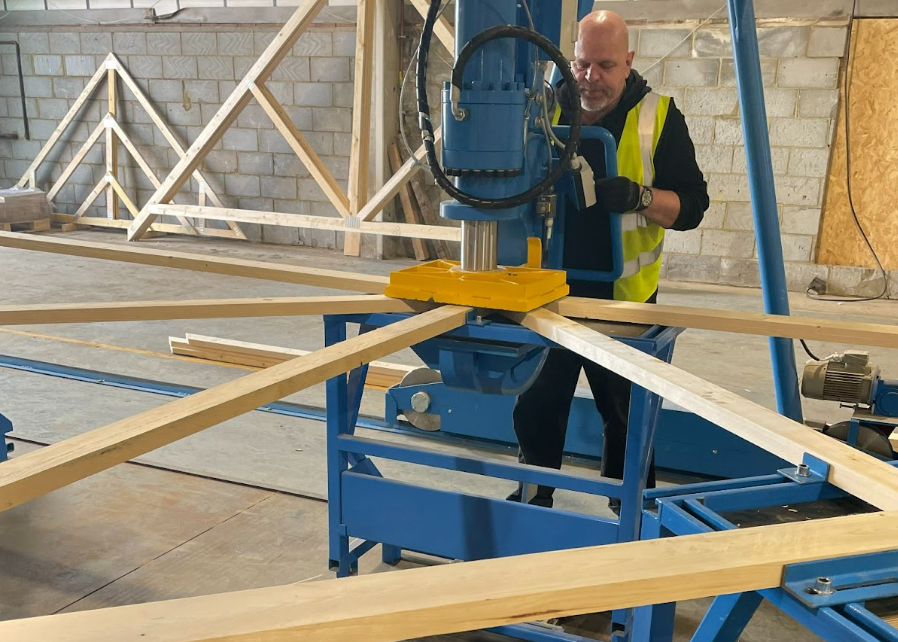
Finger jointer, pellets, biomass, solar array
Finally, we have our finger jointing machinery, biomass burner and sawdust pellet machines all of which allow us to take any potential wastage from the manufacturing process and recycle them into useful components. Whether that’s fingerjointing two offcuts together again to make a full length which can be used for another project or by turning sawdust into pellets that we burn in our bio mass boilers to fuel our offices. Read more about our ESG efforts.
In conclusion, automation of our OSM processes has led to greater accuracy and precision and it is something that we are very passionate about. Not only does it lead to greater efficiency but it is also a very sustainable way of manufacturing which has a very positive impact on the environment.
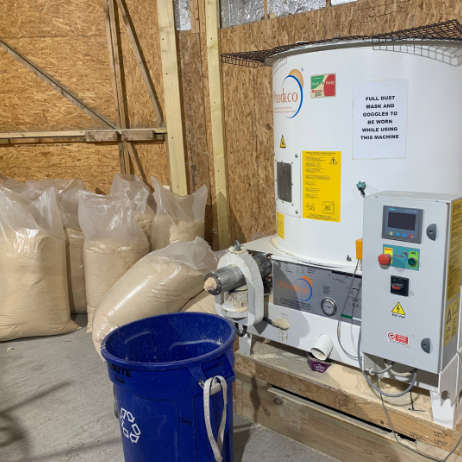
If you have any questions about us, our factory or process then get in touch! Alternatively, we would love to welcome you to come along and see our factory and machinery in action.
T: 01304 613298