For the tenth consecutive year, the market share for timber frame construction has increased. Timber frame accounts for around 23% of new home builds in the UK, and in Scotland, it is the technology of choice accounting for 85% of the housing market*
Despite this incredible influx of timber frame structures and it being one of the oldest known ‘go-to’ building methods, there are still some doubts in the industry about the longevity of these structures as well as questions of fire risks, durability, rotting, strength and more.
At OFP, our clients are constantly impressed when using timber frames as a building material for its design, performance and sustainability credentials. In this article, we aim to address the misconceptions about timber frame construction so you can have confidence when choosing timber frame for your next project.
Fire Risks
All buildings must comply with building regulations set out by the government, these include fire safety regulations.
It is a common misconception that timber frame buildings are more susceptible to fire; however, there is very little evidence to support this. Yes, timber as a material can be at risk of fire however, according to London Assembly Planning and Housing Committee, “Timber frame is an approved method of construction under the Building Regulations, and there is evidence that once constructed and maintained correctly, they pose no significantly greater risk of fire than conventionally constructed buildings.”
OFP says, “The fire resistance of any element in construction, regardless of the structure used, is the sum of its parts. Timber acts as a predictable building material with a proven charring rate – meaning all minimum resistances are calculated and comfortably adhere to regulations.”
Rotting
Similar to fire risks, wood is typically known to rot over time. Although this is true, timber frame buildings are not structured with untreated timber. The timber that is used for the construction of buildings and homes will be treated to reduce the risk of rotting, so as long as the building is not sitting in water, the risk is very small.
Speaking about rotting, OFP says, “All of our timber frames are designed to keep moisture away from the kit. Soleplates are kept above the ground floor level, and damp courses are installed. Vapour control layers and breather membranes mean that, by design, we control and prevent any risk of rotting.”
In addition, “As part of our STA Gold status, we are proud to be proven compliant when protecting our structures against rot.”
Durability
Timber has been a popular building material for thousands of years, and some of these buildings are still standing strong today. This alone is a testament to the durability of timber frame buildings.
Earlier this year, restoration work uncovered the frame of what could be Wakefield’s oldest surviving timber building:
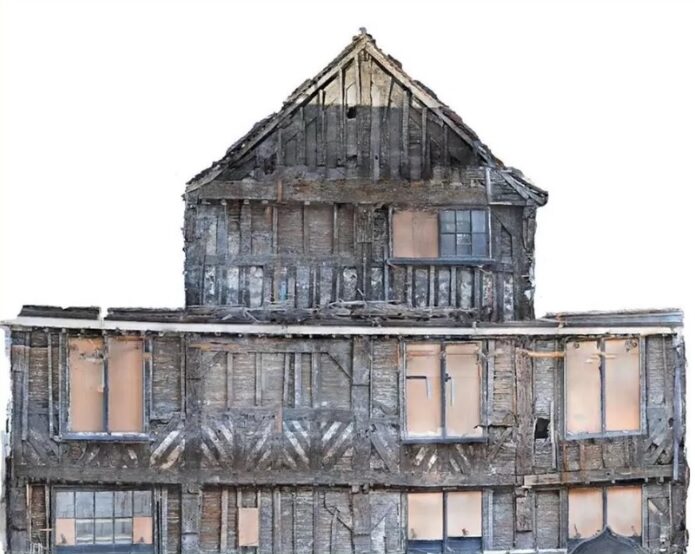
Built in 1595, this beautiful house is now believed to be the largest timber framed townhouse left in the country:
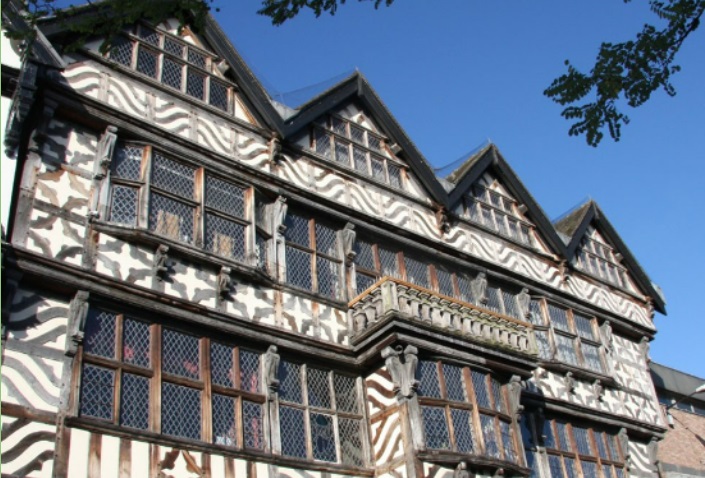
According to the STA, “provided regular maintenance is carried out, and that any repair work meets accepted levels of good workmanship, then timber framed dwellings should exhibit a performance comparable with masonry dwellings of the same age into the foreseeable future.”
Strength
Timber frame structures can be very strong and robust as long as they are designed and installed correctly and in accordance with Building Regulations.
One way to build more confidence with timber frame buildings is to further embrace Modular Methods of Construction (MMC). These forward-thinking techniques are already increasingly favourable, and they certainly support the scrutiny required to fully embrace timber frame construction (PCB Today).
Through the automation of processes and procedures, we are able to exceed levels of accuracy and efficiency like never before and ensure strength, durability, and precision. Read more about how we have adapted MMC.
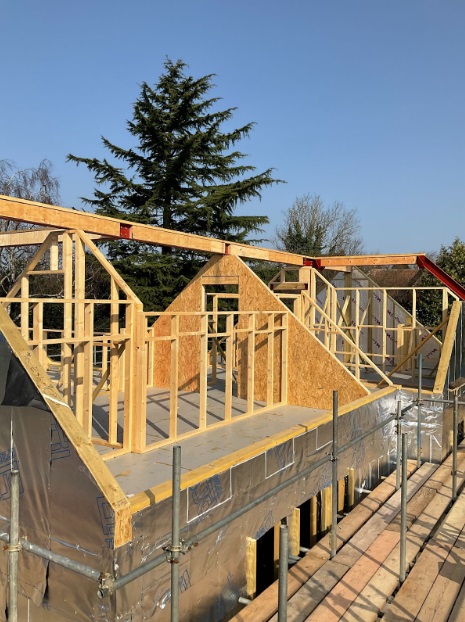

In conclusion, the doubts that the industry may have about timber frame construction can be controlled through high-quality manufacturing in line with Building Regulations coupled with correct installation.
If you are considering timber frame for your next project, then ensure you choose a manufacturer and installer with the experience, knowledge and credentials to reduce the risks of the above-mentioned.
Still not sure? Get in touch with us for a 1-2-1 or even a factory visit and let us answer your questions in more detail.
T: 01304 613298 E: info@ofptimberframe.com